The Greatest Guide To Black Hawk Parts
Table of ContentsAll about Black Hawk PartsThe Ultimate Guide To Black Hawk PartsThe Ultimate Guide To Black Hawk PartsRumored Buzz on Black Hawk Parts
KAMAN K-1200 K-Max synchropter In an alongside rotor arrangement, two straight, counter-rotating rotors are installed side-by-side on a helicopter (or transverse rotorcraft). black hawk parts. The anti-torque impact is offered by the opposing rotation of the 2 main blades. The side-by-side configuration is among the possible trip setups of a tilt-rotor airplane, when the blades are in the upright setting to provide vertical lift.It is necessary that components are developed as well as completed in a right style. As a helicopter spare parts supper in the USA, Jones Steel Products is here to develop and also finish helicopter components in a precise and also timely fashion. Jones Metal Products has more than 95 years in the hydroforming sector, a process that we make use of for a range of components in the aerospace and also protection sectors.
As a helicopter parts vendor, Jones Metal Products constantly welcomes outside organizations in for proper certifications. These outdoors organizations observe and also validate the various processes that we carry offer where we are making consistent advancements in composite manufacturing of helicopter parts. ISO 9001:2015 without Layout This certification connections to our quality management system.
When it comes to being a relied on and also valued helicopter components supplier, making advances in composite manufacturing of helicopter components comes with the territory. The procedures whereby we make helicopter components are always being boosted upon by our knowledgeable group. Our group of engineers, developers, and metalworkers have been innovating our services considering that the 1920s.
Black Hawk Parts - Questions

They can also assist you to recreate older helicopter components that originate from ceased runs all while maintaining in line with our high criteria of high quality as well as consistent manufacturing. Hydroforming, Rubber pad forming, Warmth treating, Stretch developing As a top helicopter components supplier, Jones Steel Products is pleased to function with clients in the aerospace, defense, and also airplane industries.
Helicopters are categorized as rotary wing airplane, and their rotary wing is commonly described as the primary rotor or just the blades. Unlike the a lot more common fixed wing aircraft such as a sport biplane or an airplane, the helicopter can direct upright take-off as well as landing; it can also float in a set position.
The autogiro he consequently invented bundled features of both the helicopter as well as the aircraft, although it looked like the last more. The autogiro had a rotor that worked something like a windmill. As soon as propelled by taxiing on the ground, the rotor might create additional lift; nonetheless, the autogiro was powered mostly by a conventional aircraft engine.
Examine This Report on Black Hawk Parts
To guide a helicopter, the pilot must adjust the pitch of the blades, which can be established 3 means. In the cumulative system, the pitch of all the blades affixed to the rotor equals; in the cyclic system, the pitch of each blade is designed to vary as the rotor revolves, and also the third system uses a combination of the first two.
A relevant issue takes place due to the fact that, as the helicopter moves on, the lift underneath the blades that go into the airstream first is high, however that under the blades on the contrary side of the blades is reduced. The net effect of these troubles is to destabilize the helicopter. Typically, the means of making up for these uncertain variations in lift as well as drag weblink is to make flexible blades connected to the blades by a hinge.
Torque, one more trouble linked with the physics of a turning wing, creates the helicopter fuselage (cabin) to revolve in the opposite instructions from the blades, particularly when the helicopter is relocating at low rates or hovering. To counter this response, numerous helicopters use a tail rotor, a revealed blade or ducted fan placed on the end of the tail boom typically seen on these craft.
He tried out for greater than twenty years and also finally, in 1939, flew his very first trip in a craft dubbed the VS 300. Connected to the ground with lengthy ropes, his craft flew no greater than 50 feet off the ground on its initial several visit their website trips. Also after that, there were troubles: the craft flew up, down, and also sidewards, however not onward.
Some Known Questions About Black Hawk Parts.
His concepts were eventually established into the computer-numerical-control (CNC) device tool industry that has actually revolutionized modern-day manufacturing techniques. 1 Each private tubular part is reduced by a tube cutting equipment that can be swiftly set to produce various, specific sizes as well as specified batch quantities.
For apart from minor bends, tubes are loaded with liquified salt silicate that sets as well as eliminates kinking by causing television to flex as a strong bar. The supposed water glass is after that eliminated by placing thebent tube in boiling water, which melts the internal material. Tubes that needs to be curved to match body contours is fitted over a stretch creating equipment, which stretches the steel to a specifically contoured shape.
The latter process entails infusing wax or an alloy with a low melting useful link factor into a mold and mildew or die. When the design template has been developed, it is dipped in molten steel as lot of times as necessary to achieve the thickness desired. When the component has dried, it is heated to make sure that the wax or alloy will thaw and can be put out - black hawk parts.
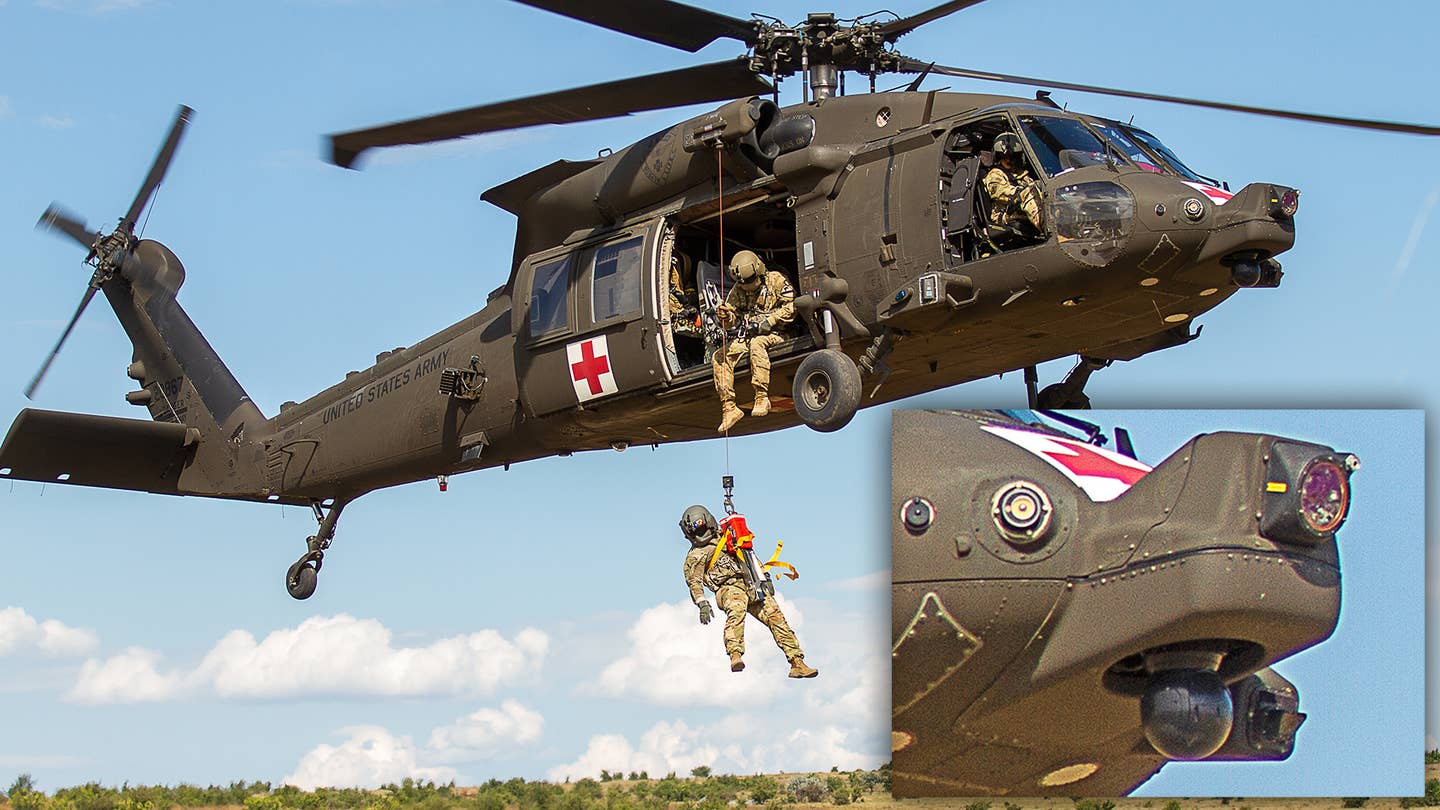